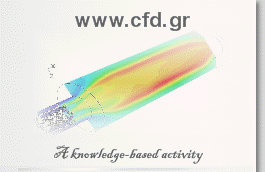
 
International
Journal Publications
1. S.Kamnis K.Kontis, Numerical studies on the
application of synthetic jets for the active control of subsonic
flow configurations. American Institute of Aeronautics &
Astronautics (AIAA 2004-2609)
2. S.Kamnis S.Gu, Numerical modelling of droplet
impingement. Journal of Physics D: Applied Physics, 38 (2005)
3664–3673
3. S.Kamnis S.Gu, Numerical modelling of propane
combustion in a high velocity oxygen–fuel thermal spray gun.
Chemical Engineering and Processing, Volume 45, Issue 4, April 2006,
Pages 246-253
4. S.Kamnis S.Gu 3-D Modelling of kerosene fuelled HVOF
thermal spray gun. Chemical Engineering Science, Volume 61,
Issue 16, August 2006, Pages 5427-5439
5. S.Kamnis S.Gu, Computational fluid dynamic modelling
of water-cooling mechanism during thermal spraying process.
Int. J. Modelling, Identification and Control, Vol. 2, No. 3, 2007
6.
N.Zeoli, S.Gu, S. Kamnis, Numerical simulation of
in-flight particle oxidation during thermal spraying.
Computers and Chemical Engineering (2007)
7. S.Kamnis S.Gu N.Zeoli Mathematical Modelling of
Inconel 718 Particles in HVOF Thermal Spraying. Surface &
Coatings Technology (2007)
8. N. Zeoli, S. Gu, S. Kamnis, Numerical modelling of
metal droplet cooling and solidification. International
Journal of Heat and Mass Transfer (2008)
9. S. Kamnis, S. Gu, T.J. Lu, C. Chen, Computational
simulation of thermally sprayed WC–Co powder. Computational
Materials Science (2008)
10. S.Gu, S.kamnis, Numerical modelling of in-flight
particle dynamics of non-spherical powder. Surface & Coatings
Technology 203 (2009) 3485–3490
11. S. Kamnis and S. Gu, Study of In-Flight and Impact
Dynamics of Nonspherical Particles from HVOF Guns. Journal of
Thermal Spray Technology (2009)
12. S. Kamnis a, S. Gu, T.J. Lu, C. Chen, Numerical
modeling the bonding mechanism of HVOF sprayed particles.
Computational Materials Science 46 (2009) 1038–1043
13. S. Gu and S. Kamnis, Bonding Mechanism from the Impact
of Thermally Sprayed Solid Particles. Metallurgical and
Materials Transactions A 2664—Volume 40A, Nov 2009
14.
S Kamnis, S Gu, T J Lu and C Chen, Numerical modelling of
sequential droplet impingements. Journal of Physics D: Applied
Physics, 41 No 16 (2008) 165303
R&D
Projects
Project: J3019E
Development of Flow Simulation and Process Control Tools for Thermal
Spray Coating (FLOSS) Partners:
Monitor Coatings Ltd,
Metallisation Ltd,
As a cost-effective method to produce wear resistant, high
temperature corrosion coating products, thermal spraying offers
greater thickness capability, no part size restrictions with minimal
noxious waste. However, complex multiphase flow generated in thermal
spraying makes process control very difficult. Supported by a
consortium including coating equipment manufacturers, service
providers, end users and research providers, this project has
proposed innovative methods to significantly reduce current costs of
established high quality coating. Closely aligned with the
competition theme, the main objectives of this project are: to
simulate the multiphase flow; to develop flow function models
integrated with CAE design and simulation tools; to develop a
process control database to mininize the operation complexity and
improve the quality of coating products.
Project: FP7-PEOPLE-IAPP-2008 Marie Curie Action 230715
Computational simulation to enhance technology development of
thermal spray coating (SimuSpray) Partners:
Southampton University,
Pyrogenesis-sa.gr
SIMUSPRAY is to develop a pan European partnership by uniting
research activities between a SME and a leading EU university. The
latest techniques in computational simulation and surface
engineering will be used or developed for solving
industry-focused engineering problems. The use of the
state-of-the-art modelling approaches will revolutionise the
technology development in protective coating and surface engineering
industry.
Project: FP7-Energy 241281
Thin Si film based hybrid solar cells on low-cost Si substrates
(ThinSi)
Partners: Stiftelsen SINTEF, Fraunhofer Institute for Solar Energy
Systems, Interuniversitair Micro-Electronica centrum VZW, Ente per
le Nuove tecnologie, l’Energia e l’Ambiente, University of
Nottingham, Oxford Instruments Plasma Technology Ltd, Elkem Solar
AS, PyroGenesis S.A, NT-MDT Europe BV, Innovative Materials
processing Technologies Ltd, Isofoton S.A.
ThinSi will develop a solar cell processing chain for
high throughput, cost-effective manufacturing of thin film silicon
based solar cells on low-cost silicon substrates. The substrates
will be made on the basis of an innovative powder-to-substrate
concept. In line with the Workprogramme topic addressed, it will
reduce the cost of solar cell modules compared to those made by the
conventional wafer based approach.
A set of innovative processes will be developed to realize the new
low-cost concept and transfer the results into production. The new
silicon based substrates will be made from low-cost material using
state-of-the art ceramics technologies. Cost effective processes for
the formation of the thin film silicon base and the complete solar
cell structure will be developed. New methods for optical
confinement will be investigated. The electronic properties of
individual solar cell materials and their interfaces as well as the
relationship between the deposition parameters and the device
properties will be analyzed using advanced characterization and
modeling.
It will also develop a better understanding of relevant materials
issues. Manufacturing procedures suitable for pilot scale production
will be developed based on an innovative process chain. The produced
solar cells will be assembled into complete modules. The project
will develop innovative technologies and equipment prototypes that
can easily be scaled up and transferred to production lines by the
end of the project. New marked opportunities for the SME and
industrial partners will be created, both as production tool
suppliers and as end-users of the technology.
Copyright ©
http://www.cfd.gr
Home |
Services | About Us |
Contact Us
 |